Automated three-dimensional warehouses are developing rapidly in China, from terminal storage to production processes, with a higher degree of automation and a high degree of integration of iot information. Widely used in pharmaceutical industry, automobile manufacturing, machinery manufacturing, tobacco industry, airport freight industry, textile industry, printing industry, chemical industry and other fields.
The application of automated warehouse is more and more extensive, and the stacker, as the key equipment of automated warehouse, plays a key role in the process of product storage and distribution. The higher the production efficiency of the enterprise, it means that the access efficiency of the piler in the roadway and the degree of refinement of the piler are more demanding.
The stacker system is composed of mechanical, electrical and software, and the three are effectively integrated. Through the software scheduling system to issue instructions to the stacker, the stacker PLC control system according to the received operation orders, storage address, shuttle back and forth in the shelf roadway, pick up goods on the conveyor or send goods to the conveyor. How to ensure the stacker operation more efficient, safe, environmental protection has become the focus of professional engineers.
1. Project background
The company integrates product research and development, engineering design, manufacturing, installation and service. The standardized, automated and large-scale broiler chickens, breeding chickens, laying hens, pig farm projects and greenhouse temperature control projects have the international advanced level. In order to promote production capacity and improve the logistics system, the enterprise specially invited our institute to plan and construct an automated three-dimensional warehouse for the new manufacturing center and R & D center project.
The automatic three-dimensional warehouse stacker is composed of mechanical structure (including upper and lower beams and columns), loading platform, operating mechanism, lifting mechanism, cargo fork expansion mechanism and electronic control device.
2. Speed regulation requirements for horizontal shaft of piler
Due to the particularity of the mechanical structure of the piler, the bending moment of the column caused by the loading platform and the cargo and the horizontal inertia force generated by the piler's acceleration and deceleration during operation will cause the column to bend and deform in the roadway plane, affecting the stability and reliability of the piler's operation, and making the debugging of the piler's running speed and acceleration in the horizontal axis direction complicated.
The speed regulation of the horizontal axis inverter should meet the stable acceleration process of the stacker, increase the speed to a larger speed in a short time, and accurately stop at the shortest deceleration distance when running at high speed to the destination address, and the stacker should run reliably and smoothly in the whole process. Performance parameters of the stacker: greater load capacity of 1 000 kg, greater speed of the operating shaft 160 m/min, and acceleration of the operating shaft 0.5 m/s2.
3. Stacker control system
The lower control of the stacker control system is realized by the asynchronous motor driven by the frequency converter. The speed adjustment of the horizontal axis, vertical axis and cargo fork of the stacker is controlled by the asynchronous motor by the frequency converter. The position value fed back by the laser ranging sensor, barcode locator and value encoder is used to locate the stacker.
3.1 Network topology of the control system
Through PN/IE(Profinet) network protocol, the PLC is connected with the frequency converter, encoder and laser ranging sensor. The frequency converter receives the start and stop command issued by the PLC through the fieldbus, and feed-back the online data current, voltage and motor running state of the frequency converter to the upper control system. In this project, the operation signal of the inverter is collected into PLC as the protection program for judging the complete shutdown of the horizontal shaft of the stacker.
3.2 Inverter bus parameter configuration
After the hardware configuration of the stacker control system is completed, the input and output (I/O) configuration file of the inverter is matched with the PLC input and output image area, and the output area of the PLC corresponds to the input area of the inverter, and the input area of the PLC corresponds to the output area of the inverter. The inverter receives the frequency pulse speed regulation or the speed regulation by changing the parameter status word and gives feedback information.
4. Stacker control system function
The horizontal axis speed regulation of the stacker control system is divided into manual operation speed regulation and automatic operation speed regulation. The manual speed regulation is controlled by the operation handle on the stacker to advance at low speed, retreat at low speed, advance at high speed and retreat at high speed. The forced speed change switch is provided on the ground, and the operation is switched to low speed after the high-speed operation reaches the end of the roadway. Automatic speed regulation is that the stacker automatically accelerates from the stationary state to high-speed operation according to the running distance after receiving the warehousing and discharging instructions in the online mode, and then decelerates to the accurate stop after reaching the target cargo location.
4.1 After the slope is set, smooth and slow down of the uniform speed section are adjusted, and the proportional gain SPG, time constant SIT and filter coefficient SFC are changed to make the uniform speed section stable. During debugging, it was found that under PID parameter operation with uniform speed and stability, the horizontal axis was stable in the initial start-up stage, uniform speed operation and deceleration stage, but the deceleration distance of the horizontal axis was extended. At the same speed, the deceleration stopping distance fluctuated greatly, and the deceleration was not enough in the final stage of the shutdown.
In order to solve this problem, the efficiency of horizontal shaft speed regulation is improved by adjusting the PID parameters of speed ring, and the adjustment effect of speed ring PID is achieved.
5. Apply
The swing of the piler column has a great relationship with the speed regulation parameters of the horizontal axis. If the speed regulation of the horizontal axis is started too fast or stopped too hard, the swing amplitude of the piler column will be large, resulting in cargo displacement on the loading platform and serious wear of the horizontal shaft drive mechanism, reducing the safety of the piler and shortening its service time.
Therefore, in order to meet the requirements of production efficiency, the stability of the speed regulation process of the horizontal shaft of the stacker must be ensured after the speed regulation is completed. By using the debugging software of vector frequency converter and its stability, the speed regulation efficiency of horizontal axis can be improved, and the maintenance is convenient, which lays a good foundation for later stable application.
-
What are the types of stackers?2022-06-21
-
What are the advantages of stackers2022-06-23
-
Automatic stacker manufacturers: Warehouse stacker machine speed control details2022-06-16
-
Intelligent stacker manufacturer: The use of the stacker with the shuttle car system2022-06-17
-
Information about secure storage and stacking in warehouses2021-03-03
-
Do you need VNA narrow lane shelves? Advantages and characteristics2022-10-21
-
5 features to help you operate your forklift safely2021-04-08
-
7 Energy Considerations for Material Handling Automation?2021-05-12
No. 95 Yuchang Road, Niuhu Community, Guanlan Street, Longhua District, Shenzhen, China
Building 208, New Sun Technology Industrial Park, Tangxia Town, Dongguan City, China
0769-82861482
0755-89500671
0769-82862446
Facebook+8618098943383
Whatsapp+8618098943383
huangqj@xrdsz.com
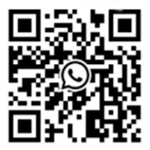